Деталиновости
Оптимизация системы смазки
Автор:Shuangcheng Время:2025-03-21 23:25:44 Просмотры:126
Система смазки гидравлического камерного фильтра играет важную роль в обеспечении бесперебойной работы его механических компонентов, уменьшении трения, уменьшении износа и продлении срока службы оборудования. Оптимизированная система смазки может улучшить общую производительность, надежность и энергоэффективность фильтра давления. В этой статье предлагается комплексная оптимизация системы смазки гидравлического камерного фильтра.
Текущие проблемы смазочных систем
2.1 Недостаточное снабжение смазочными материалами
Распределение неравномерно: в некоторых фильтрах существующие системы смазки могут не распределять смазочные материалы равномерно по всем движущимся компонентам. Например, в многопластинчатых фильтрах некоторые шарнирные контакты или скользящие поверхности могут получать меньше смазки, чем другие шарнирные контакты или поверхности, что приводит к ускорению износа в этих областях.
Недостаточное количество: количество поставляемых смазочных материалов может быть недостаточным, особенно во время непрерывной работы с высокой нагрузкой. Это может привести к увеличению трения между компонентами, генерировать больше тепла и может привести к отказу компонентов.
2.2 Загрязнение смазочными материалами
Вход твердых частиц: в промышленной среде пыль, грязь и мелкие металлические частицы могут попасть в систему смазки. Например, при эксплуатации фильтров, связанных с добычей, мелкие частицы руды могут проникать в смазочные материалы через отверстие на уплотнении или во время технического обслуживания. Эти твердые частицы могут использоваться в качестве абразива, увеличивая износ и снижая эффективность смазки.
Загрязнение воды: вода может поступать в систему смазки из окружающей атмосферы или через утечку гидравлических элементов. На очистных сооружениях, где фильтр подвергается воздействию влажной среды, вода смешивается с смазочными материалами, что приводит к коррозии металлических деталей и эмульсии смазочных материалов, что снижает их смазочные свойства.
2.3 Неэффективные методы смазки
Ручная смазка: некоторые фильтры по - прежнему полагаются на ручную смазку, которая занимает много времени и непоследовательна. Операторы могут не смазывать все детали с правильными интервалами, и количество смазочных материалов может сильно различаться. Недостаточная точность ручной смазки может привести к чрезмерной смазке в некоторых областях (расточительству смазочных материалов и привлечению большего количества грязи), в то время как другие области недостаточно смазаны.
Одноточечная смазка: использование одноточечной смазочной системы для нескольких компонентов может быть недостаточным для удовлетворения конкретных требований к смазке для каждого компонента. Различные движущиеся компоненты в фильтре давления, такие как гидравлические цилиндры, цепи и подшипники, имеют разные скорости, нагрузки и рабочие температуры, поэтому требуют разных стратегий смазки.
3. Меры по оптимизации
3.1 Выбор смазочных материалов и управление ими
Правильный уровень смазки: выберите смазку, подходящую для конкретных условий работы фильтра. Рассмотрим такие факторы, как тип механических компонентов (например, являются ли они подшипниками, шестернями или гидравлическими цилиндрами), диапазон рабочих температур, приложенная нагрузка и присутствие загрязняющих веществ в окружающей среде. Для высокотемпературных применений можно выбрать синтетическую смазку с высокой термической стабильностью. В пыльной среде предпочтение отдается смазочным материалам с хорошей антифрикционной стойкостью и свойствами суспензии.
Фильтрация и очистка смазочных материалов: установка высокоэффективной системы фильтрации в смазочных контурах для удаления твердых частиц и влаги. Можно использовать многоступенчатые фильтры, начальные грубые фильтры используются для удаления крупных частиц, а тонкие фильтры используются для захвата небольших загрязнителей. Кроме того, рассмотрим возможность использования сепаратора воды для удаления любой влаги, присутствующей в смазке. Состояние смазочных материалов регулярно контролируется с использованием таких методов, как анализ масла, для определения того, когда требуется их замена или дальнейшая очистка.
3.2 Улучшение распределения смазочных материалов
Многоточечная автоматическая система смазки: замена существующих неэффективных методов смазки многоточечной автоматической системой смазки. Система может быть запрограммирована, чтобы обеспечить достаточное количество смазочных материалов для каждого ключевого движущегося компонента с заданными интервалами. Например, он может быть сконфигурирован как шарнирная точка автономной смазочной фильтрующей пластины, поршневой стержень гидравлического цилиндра и подшипник конвейерной системы. Автоматизированная система обеспечивает последовательную и точную смазку и снижает риск недостаточной или чрезмерной смазки.
Конструкция смазочных трубопроводов: оптимизация конструкции смазочных трубопроводов для обеспечения равномерного распределения смазочных материалов. Используйте подходящие трубопроводы для поддержания требуемой скорости потока и давления. Установите клапан управления расходом в ключевой точке смазочного трубопровода, чтобы регулировать количество смазочного материала, достигающего каждого компонента. Убедитесь, что проводка смазочных трубопроводов правильно, чтобы избежать скручивания или блокировки, которые могут нарушить поток смазочных материалов.
3.3 Закрытие и защита
Усиленное уплотнение: обновление уплотнений вокруг движущихся частей для предотвращения попадания загрязняющих веществ в систему смазки. Например, на гидравлических цилиндрах и подшипниках используются высококачественные губчатые или механические уплотнения. Эти уплотнения должны выбираться в соответствии с условиями эксплуатации (например, давлением, температурой и скоростью). Периодически проверять и заменять уплотнения с признаками износа или повреждения для поддержания их эффективности.
Защитные крышки и колпаки: Установка защитных крышек и колпаков на наружные движущиеся части для уменьшения пыли, грязи и влаги, которые могут достигать системы смазки. Для элементов цепной передачи, пожалуйста, поместите их в защитный чехол. Эти крышки не только защищают смазочные системы, но и повышают безопасность работы фильтров.
3.4 Мониторинг и техническое обслуживание
Датчики мониторинга состояния: Установите датчики для мониторинга состояния смазочной системы, такие как датчики температуры для обнаружения аномального нагрева, вызванного плохой смазкой, датчики давления для обеспечения надлежащего потока смазки, датчики вибрации для выявления любых чрезмерных вибраций, вызванных изношенными или недостаточно смазанными компонентами. Подключите эти датчики к центральной системе мониторинга, которая может предупредить оператора о любой проблеме.
План периодического обслуживания: разработка подробного плана периодического обслуживания смазочных систем. Это включает такие задачи, как проверка уровня жидкости в смазочных материалах, проверка фильтров, замена изношенных уплотнений и калибровка автоматических систем смазки. Подготовка обслуживающего персонала для точного и эффективного выполнения этих задач.
4. Ожидаемые выгоды оптимизации
4.1 Продление срока службы компонентов
Обеспечивая надлежащую смазку и уменьшая трение, скорость износа механических компонентов, таких как подшипники, шестерни и гидравлические цилиндры, будет значительно снижена. Это может значительно продлить срок службы, уменьшить частоту замены компонентов и соответствующее время простоя.
4.2 Повышение энергоэффективности
Благодаря оптимизированной смазке, уменьшается трение, что означает, что фильтр давления требует меньше энергии для работы. Это может снизить потребление электроэнергии и, следовательно, сэкономить деньги с течением времени.
4.3 Повышение надежности
Оптимизированная система смазки в сочетании с эффективными мерами мониторинга и технического обслуживания может свести к минимуму риск непредвиденных сбоев. Фильтры под давлением будут работать более плавно и стабильно, повышая общую надежность используемых ими промышленных процессов.
4.4 Экономия затрат
Сочетание увеличения срока службы компонентов, снижения энергопотребления и повышения надежности может сэкономить общие затраты. Меньшее количество замен деталей, меньшие затраты на энергию и меньшее время простоя превращаются в более экономичную работу гидравлических камерных фильтров.
5. Выводы
Оптимизация системы смазки гидравлического камерного фильтра имеет решающее значение для повышения ее производительности, надежности и рентабельности. Решая текущие проблемы в системах смазки, осуществляя соответствующие меры оптимизации и получая ожидаемые выгоды, фильтры под давлением могут работать более эффективно в различных промышленных применениях, уменьшая проблемы с обслуживанием. Регулярный мониторинг и постоянное совершенствование смазочных систем также имеют решающее значение для обеспечения их долгосрочной эффективности.
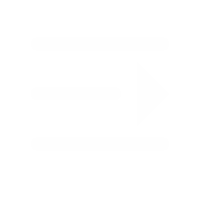
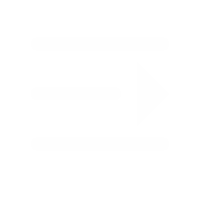
—— Контакт:Manager
—— Тел:+86 16632826789
—— Почта:sales@hbscfilterpress.com
—— Сайт:https://www.hbscfilterpress.com
—— Адрес:Западная зона экономической зоны развития, уезд Фучэн, город Хэншуй, провинция Хэбэй.