NewsDetails
Comprehensive Guide to the Operation and Maintenance of Hydraulic Chamber Filter Press
author:Shuangcheng time:2025-03-21 23:32:47 Click:111
1. Introduction
Hydraulic chamber filter presses are widely used in various industries for solid - liquid separation. Proper operation and maintenance are crucial to ensure their efficient performance, long - term reliability, and to avoid costly breakdowns. This guide provides a detailed overview of all aspects related to the operation and maintenance of hydraulic chamber filter presses.
2. Pre - operation Preparation
2.1 Equipment Inspection
Visual Inspection: Before starting the filter press, conduct a thorough visual inspection. Check the filter plates for any signs of damage, such as cracks, chips, or warping. Inspect the filter cloth for tears, holes, or excessive wear. Ensure that all the connections, including hydraulic hoses, pipes, and electrical wires, are secure and free from leaks or exposed conductors.
Hydraulic System Check: Examine the hydraulic oil level in the reservoir. It should be within the recommended range. Check for any signs of oil contamination, such as discoloration or the presence of foreign particles. Inspect the hydraulic pump, valves, and cylinders for leaks or abnormal noises. Test the functionality of the pressure gauge and other control devices to ensure accurate readings and proper operation.
Mechanical Components: Check the moving parts of the filter press, such as the filter plate moving mechanism, hinges, and conveyor belts (if applicable). Ensure that they are properly lubricated and move smoothly without any jamming or binding.
2.2 Slurry Preparation
Slurry Characteristics: Understand the properties of the slurry to be processed, including its solid - content, particle size distribution, viscosity, and chemical composition. This information is essential for setting the appropriate operating parameters of the filter press, such as pressure, filtration time, and feed rate.
Slurry Pre - treatment: In some cases, the slurry may require pre - treatment to improve the filtration efficiency. This could involve processes such as dilution, coagulation, or flocculation. For example, adding a flocculant to the slurry can help the fine solid particles agglomerate, making them easier to separate during filtration.
3. Operation Process
3.1 Starting the Filter Press
Power On: Switch on the electrical power supply to the filter press control panel. Ensure that all the electrical components are functioning properly and that there are no error messages on the display.
Hydraulic System Activation: Start the hydraulic pump. Allow the hydraulic system to build up pressure gradually. Monitor the pressure gauge to ensure that the pressure reaches the set value for the initial stage of operation.
Filter Plate Closing: Use the control panel to activate the filter plate closing mechanism. The filter plates should move smoothly and close evenly. Check for any misalignment or gaps between the plates during the closing process. Once the plates are fully closed, lock the plate - locking mechanism.
3.2 Feeding the Slurry
Slurry Pump Start - up: Start the slurry pump. Adjust the feed rate according to the characteristics of the slurry and the capacity of the filter press. Initially, a lower feed rate may be used to allow the filter cloth to be evenly coated with the solid particles. As the filtration process progresses, the feed rate can be gradually increased.
Monitoring the Filtration Process: Continuously monitor the pressure in the filter chamber, the flow rate of the filtrate, and the appearance of the filter cake. The pressure in the chamber should increase steadily as the solid particles accumulate on the filter cloth. If the pressure rises too rapidly or exceeds the set maximum value, it may indicate a blockage in the filter cloth or an improper feed rate. Adjust the feed rate or take appropriate measures to clear the blockage.
3.3 Filtration and Dewatering
Maintaining Pressure: During the filtration and dewatering phase, maintain a stable pressure in the filter chamber. The pressure can be adjusted using the pressure - regulating valves in the hydraulic system. Higher pressures are generally required for achieving a lower moisture content in the filter cake, but care should be taken not to exceed the maximum pressure rating of the filter press.
Filtrate Collection: Collect the filtrate in a suitable container. Monitor the quality of the filtrate. If the filtrate contains excessive solids, it may indicate a problem with the filter cloth, such as a tear or improper installation. In such cases, stop the filtration process and inspect the filter cloth.
3.4 Filter Cake Discharge
Pressure Relief: Once the desired moisture content in the filter cake is achieved, start the pressure - relief process. Slowly open the pressure - relief valves in the hydraulic system to release the pressure in the filter chamber. Ensure that the pressure is completely relieved before proceeding to the next step.
Filter Plate Opening: Use the control panel to activate the filter plate opening mechanism. The filter plates should open smoothly, allowing the filter cake to fall by gravity or with the assistance of a mechanical device, such as a scraper or a conveyor belt. If the filter cake does not discharge easily, check for any adhesion to the filter cloth or filter plates and take appropriate measures to remove it.
4. Post - operation Procedures
4.1 Equipment Cleaning
Filter Plate and Filter Cloth Cleaning: After the filter cake is discharged, clean the filter plates and filter cloth thoroughly. Use a high - pressure water jet or a suitable cleaning agent to remove any remaining solid particles on the filter plates and filter cloth. Ensure that the filter cloth is free from clogging to maintain its filtration efficiency for the next operation.
Hydraulic System Cleaning: Periodically clean the hydraulic system, including the reservoir, pipes, and valves. Remove any accumulated dirt, debris, or contaminants from the system. Replace the hydraulic oil filter regularly to keep the hydraulic oil clean.
4.2 Shut - down and Storage
Power Off: After cleaning, switch off the electrical power supply to the filter press. Disconnect any external connections, such as the slurry feed hose and the filtrate discharge pipe.
Equipment Storage: If the filter press is not going to be used for an extended period, store it in a clean, dry, and protected area. Cover the equipment to prevent dust and dirt from accumulating on it. Check the equipment periodically during storage to ensure that there are no signs of corrosion or damage.
5. Maintenance and Troubleshooting
5.1 Regular Maintenance
Lubrication: Regularly lubricate all the moving parts of the filter press, including hinges, bearings, and the filter plate moving mechanism. Use a suitable lubricant according to the manufacturer's recommendations. Lubrication helps to reduce friction, minimize wear, and ensure smooth operation of the equipment.
Hydraulic System Maintenance: Check the hydraulic oil level and quality regularly. Replace the hydraulic oil at the recommended intervals. Inspect the hydraulic hoses, pipes, and fittings for leaks or damage. Tighten any loose connections. Test the performance of the hydraulic pump, valves, and cylinders periodically to ensure their proper functioning.
Filter Cloth Replacement: Monitor the condition of the filter cloth. Replace the filter cloth when it is severely worn, torn, or clogged. Choose a filter cloth with the appropriate properties, such as pore size and chemical resistance, for the specific slurry being processed.
5.2 Troubleshooting Common Problems
Leakage: If there is leakage in the filter press, check for worn - out gaskets between the filter plates, damaged filter cloth, or loose connections in the hydraulic system. Replace the gaskets or filter cloth as needed and tighten the connections.
Low Filtration Efficiency: A low filtration efficiency may be caused by a clogged filter cloth, improper feed rate, or insufficient pressure. Clean or replace the filter cloth, adjust the feed rate, and check the pressure settings in the hydraulic system.
Abnormal Noises: Abnormal noises from the filter press may indicate problems with the moving parts, such as worn - out bearings or a misaligned filter plate. Inspect the moving parts, replace any damaged components, and ensure proper alignment.
6. Safety Precautions
6.1 Personal Safety
Training: Ensure that all operators are properly trained in the operation and maintenance of the filter press. They should be familiar with the safety procedures and emergency shutdown mechanisms.
Protective Equipment: Operators should wear appropriate personal protective equipment, such as safety glasses, gloves, and hard hats, when working around the filter press.
Lock - out/Tag - out: Before performing any maintenance or repair work on the filter press, follow the lock - out/tag - out procedure to prevent accidental startup of the equipment.
6.2 Equipment Safety
Over - pressure Protection: Install over - pressure protection devices, such as pressure - relief valves, in the hydraulic system. These devices should be regularly tested to ensure their proper functioning.
Electrical Safety: Ensure that the electrical wiring and components of the filter press are properly installed and grounded. Use electrical safety devices, such as circuit breakers and ground - fault interrupters, to prevent electrical accidents.
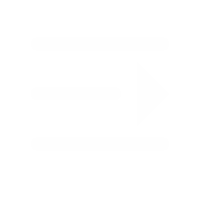
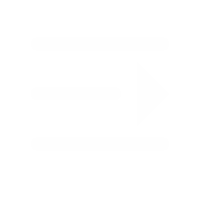
—— Contact:Manager
—— Tel:+86 16632826789
—— Email:sales@hbscfilterpress.com
—— Url:https://www.hbscfilterpress.com
—— Address:West Zone of Economic Development Zone, Fucheng County, Hengshui City, Hebei Province