NewsDetails
High-Pressure Diaphragm Filter Press: Revolutionizing Filtration with Unmatched High-Pressure Processing Capabilities
author:Shuangcheng time:2025-05-18 19:51:40 Click:163
In the realm of industrial solid-liquid separation, equipment processing capacity directly determines production efficiency and resource utilization. The High-Pressure Diaphragm Filter Press (HPDP Filter Press) disrupts traditional filtration paradigms with its exceptional high-pressure capabilities, delivering transformative breakthroughs across industries. This article delves into its technical principles, core advantages, and application essentials to help you grasp cutting-edge trends in industrial filtration.
1. Introduction: Technological Innovation Driven by High-Pressure Filtration Demands
Solid-liquid separation is a pivotal step in resource recovery, wastewater treatment, and product purification within industrial production. Traditional filtration equipment, constrained by insufficient pressure and low separation efficiency, struggles to handle high-viscosity or high-impurity materials. The HPDP Filter Press, leveraging ultra-high pressure and innovative diaphragm technology, achieves deep solid-liquid separation, offering irreplaceable value in sectors like chemicals, environmental protection, and mining. It stands as the cornerstone of industrial filtration upgrades.
2. Technical Analysis of the High-Pressure Diaphragm Filter Press
2.1 Structure and Core Components
The HPDP Filter Press consists of:
Filter Plate Assembly: Made from high-strength materials, its surface is covered with filter cloths to form filtration chambers.
Diaphragm Layer: Composed of elastic rubber or polymer materials, it expands under pressure to apply secondary compression.
Hydraulic System: Delivers pressures up to tens of MPa, ensuring tight filter plate closure and powerful diaphragm squeezing.
Intelligent Control System: Monitors and adjusts operational parameters for automated, precise filtration.
2.2 High-Pressure-Driven Operating Principles
During operation, material is pumped into sealed filtration chambers under high pressure. Liquid permeates through filter cloths and exits, while solid particles are retained. Once a preliminary filter cake forms, high-pressure media (e.g., water, air) is injected into the diaphragm layer, causing it to expand and squeeze the cake, expelling residual liquid. This dual-action "filtration + high-pressure squeezing" significantly enhances separation efficiency and precision.
3. Core Advantages of High-Pressure Processing
3.1 High-Speed Filtration
Compared to conventional filter presses, the HPDP Filter Press shortens filtration cycles through high-pressure driving and diaphragm squeezing. Elevated pressure accelerates liquid permeation, while mechanical diaphragm compression forces residual liquid from cake pores, drastically increasing throughput per unit time.
3.2 Deep Separation Performance
Ultra-high pressure, coupled with precision filter cloths, achieves profound solid-liquid separation. Resulting filter cakes exhibit dramatically reduced moisture content, and filtrate clarity improves significantly, lowering costs and energy consumption in subsequent drying and purification steps.
3.3 Broad Material Adaptability
Whether handling high-viscosity sludge, fine chemical slurries, or high-concentration mineral suspensions, the HPDP Filter Press adapts to diverse material properties by adjusting pressure parameters and diaphragm characteristics, ensuring stable and efficient separation.
4. Key Factors Influencing High-Pressure Efficiency
4.1 Material Performance and Pressure Resistance
Filter Plates: Must balance high strength and corrosion resistance (e.g., polypropylene resists chemicals but has limited pressure tolerance; reinforced composites withstand higher pressures).
Diaphragm Materials: Elasticity and fatigue resistance directly impact squeezing efficiency. High-quality diaphragms ensure long-term stable operation.
4.2 Process Parameter Optimization
Pressure Control: Excessive pressure may damage filter cloths or plates; thresholds must be set based on material properties.
Squeezing Duration: Extending diaphragm squeezing time further reduces cake moisture but requires balancing energy consumption and efficiency.
Temperature Management: Heat-resistant materials are essential in high-temperature environments to prevent diaphragm deformation or filter cloth aging.
4.3 Equipment Maintenance and Care
Regularly inspect hydraulic system seals, clean filter plate surfaces, and monitor diaphragm wear. Prompt replacement of aged components prevents pressure leaks and filtration chamber failures, ensuring long-term stability.
5. Industry Application Guidelines for HPDP Filter Presses
5.1 Define Application Requirements
Based on industry characteristics (e.g., environmental protection, chemicals, mining) and material properties, determine pressure ratings, filter plate sizes, and automation levels. High-viscosity materials require higher pressure configurations, while fine chemical separations demand stricter filtrate purity.
5.2 Supplier Selection Criteria
Prioritize suppliers with high-pressure equipment R&D capabilities, comprehensive quality certifications, and reliable after-sales support. Evaluate pressure stability, diaphragm technology, and response speed to ensure long-term operational reliability.
5.3 Equipment Selection and Comparison
Compare pressure parameters, energy consumption, and intelligent features across brands. Focus on core indicators like diaphragm lifespan and filter plate strength, making science-based decisions aligned with budget and production needs.
6. Conclusion: High-Pressure Technology Driving the Future of Filtration
The HPDP Filter Press redefines industrial filtration standards with its exceptional high-pressure capabilities. From efficiency gains to deep separation, material adaptability, and energy optimization, its technological advantages are driving production transformations in chemicals, environmental protection, and mining. As materials science and intelligent control technologies advance, future HPDP Filter Presses will evolve toward higher pressures, lower energy consumption, and full automation. Enterprises should embrace this technological trend, adopting efficient equipment to secure competitive advantages and environmental leadership in industrial filtration.
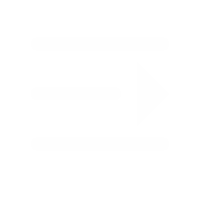
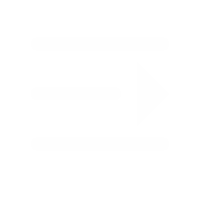
—— Contact:Manager
—— Tel:+86 16632826789
—— Email:sales@hbscfilterpress.com
—— Url:https://www.hbscfilterpress.com
—— Address:West Zone of Economic Development Zone, Fucheng County, Hengshui City, Hebei Province