NewsDetails
How Different Industries Can Effectively Utilize Plate and Frame Filter Presses: Application Scenarios and Key Selection Considerations
author:Shuangcheng time:2025-06-13 08:00:52 Click:98
In the realm of industrial production, the Plate and Frame Filter Press stands out as an indispensable piece of key equipment across numerous industries, thanks to its unique structural design and powerful solid-liquid separation capabilities. Its high separation efficiency and flexible operation modes cater to a wide range of production demands. However, given the vast differences in material properties, production processes, and quality standards among various industries, selecting the right type of plate and frame filter press and using it scientifically according to industry-specific characteristics is crucial for maximizing the equipment's effectiveness.
I. In-depth Analysis of Typical Industry Application Scenarios
(A) Chemical Industry: Meeting the Stringent Challenges of Complex Materials
In chemical production, plate and frame filter presses are widely employed in processes such as the separation of fine chemical products and wastewater treatment. Chemical materials often possess properties like strong corrosiveness, high toxicity, or being flammable and explosive. Additionally, there are stringent requirements for the purity and impurity content of the separated products. For instance, in the production of certain acid-base chemical products, ordinary filter plates and cloths are highly susceptible to corrosion, leading to equipment leakage and reduced separation efficiency. During wastewater treatment, there is a need to precisely separate harmful substances like heavy metal ions, imposing demanding requirements on filtration accuracy.
To address these challenges, the chemical industry should opt for materials with excellent corrosion resistance, such as polypropylene or stainless steel for filter plates, and polytetrafluoroethylene for filter cloths, which can effectively resist strong acid and alkali erosion. Furthermore, adopting special sealing designs, such as double-sealing structures, can enhance the equipment's tightness, preventing material leakage and potential safety accidents and environmental pollution.
(B) Food Industry: Upholding Stringent Hygiene and Safety Standards
In the food processing sector, plate and frame filter presses are commonly used in processes like juice clarification, starch dewatering, and fermentation broth separation. This industry has extremely strict hygiene standards for equipment, as any impurity residue or material contamination from the equipment can lead to food safety issues. For example, in juice production, if the filter cloth does not meet food-grade standards, harmful substances may leach into the juice. Additionally, if there are cleaning dead spots on the equipment surface, residual materials can easily breed bacteria, affecting product quality.
Therefore, the food industry must select materials that comply with food hygiene standards, such as food-grade polypropylene filter plates and edible-grade filter cloths. Meanwhile, the equipment design should prioritize ease of cleaning, featuring smooth surfaces and dead-spot-free structures to facilitate quick and thorough cleaning after production, thereby avoiding material residue. Regular disinfection of the equipment is also an essential measure to ensure food safety.
(C) Mining Industry: Efficiently Handling Large-Scale Coarse and Hard Materials
In mining production, plate and frame filter presses are mainly used in operations such as tailings treatment, mineral concentration, and concentrate dewatering. Ore materials are generally characterized by large, hard particles, high processing volumes, and strong abrasiveness. For instance, in tailings dewatering, a large amount of tailings needs to undergo solid-liquid separation within a short time, and the sharp particles in the tailings can quickly wear out the filter plates and cloths. During mineral concentration, the high concentration of ore slurry poses higher requirements for the equipment's pressure-bearing capacity.
To meet the demands of mining production, it is necessary to equip the filter press with high-strength filter plates, such as those made of reinforced polypropylene with optimized internal structures to enhance their compressive strength and wear resistance. Simultaneously, selecting highly wear-resistant filter cloths and matching them with wear-resistant components, such as thickened filter plate frames and wear-resistant inlet pipes, can extend the equipment's service life. Additionally, optimizing the equipment's feeding system can improve material processing efficiency and meet the needs of large-scale mining production.
(D) Wastewater Treatment Industry: Overcoming the Challenges of Sludge Treatment
In the wastewater treatment field, plate and frame filter presses are core equipment for sludge dewatering and pre-treatment for water reuse. Sludge has a complex composition, containing a large amount of organic matter, microorganisms, heavy metals, etc., and has a high water content and poor fluidity, posing significant challenges for solid-liquid separation. For example, in municipal sludge dewatering, if the sludge water content cannot be effectively reduced, it will increase the subsequent sludge disposal costs. In industrial sludge, if harmful substances are not thoroughly separated, they can pollute the environment.
To address the characteristics of sludge, it is necessary to select special filter cloths with high air permeability and high retention rates to improve dewatering efficiency and separation effects. Meanwhile, adopting a high-pressure squeezing function and gradually increasing the pressure can further squeeze out water from the sludge, reducing its water content. Additionally, optimizing the equipment's feeding method and filtration process can better adapt to the treatment needs of sludge with different properties.
II. Key Considerations for Precise Selection
(A) Determining Processing Capacity Based on Production Scale
When selecting a plate and frame filter press, the first consideration should be the production scale and expected filtration volume. Enterprises with large production scales and high filtration demands should choose equipment with a large filtration area, a high number of filter plates, and strong processing capacity. Generally, the required filtration area can be calculated based on parameters such as the volume of material to be processed per unit time, solid content, etc., combined with the equipment's filtration rate. Meanwhile, the selection of filter plate size should also comprehensively consider factors such as equipment installation space and operational convenience to ensure that the equipment can not only meet production needs but also facilitate daily maintenance and management.
(B) Adapting Equipment Parameters According to Material Characteristics
The acidity, alkalinity, viscosity, and particle size of materials directly influence the selection of equipment materials, filter cloth types, and filtration pressures. For acidic or alkaline materials, filter plates and cloths made of corrosion-resistant materials should be chosen. High-viscosity materials have poor fluidity and require higher filtration pressures, along with filter cloths with good air permeability to reduce filtration resistance. For materials with small particle sizes, finer filter cloth pore sizes are needed to ensure separation accuracy. Therefore, before selection, a comprehensive analysis and testing of material characteristics should be conducted to ensure a perfect match between the equipment and the materials.
(C) Balancing Automation Levels to Meet Industry Needs
Plate and frame filter presses are available in manual, semi-automatic, and fully automatic types, each with its own advantages and disadvantages. Manual equipment is simple to operate and has low costs but involves high labor intensity and low efficiency, making it suitable for small-scale production or experimental scenarios. Semi-automatic equipment partially automates operations, such as automatic filter plate separation and automatic feeding, which can improve production efficiency and reduce labor costs, making it suitable for medium-scale production. Fully automatic equipment features full-process automation, including automatic feeding, squeezing, washing, and unloading, offering high production efficiency and stable operation but with higher equipment investment costs. Different industries should reasonably select equipment with an appropriate automation level based on factors such as their production rhythm, labor costs, and production stability requirements.
(D) Making Decisions Based on a Comprehensive Assessment of Budget and Post-Purchase Costs
In addition to the equipment procurement cost, maintenance costs, energy consumption costs, and other post-purchase expenses should also be considered. High-performance, high-quality equipment may have a higher purchase price but lower failure rates and longer service lives, resulting in relatively lower post-purchase maintenance costs. Although equipment with a high automation level has a larger initial investment, it can reduce labor costs and improve production efficiency, making it more cost-effective in the long run. Additionally, the equipment's energy consumption level is also an important consideration, as energy-saving equipment can reduce energy consumption during production and save operating costs. Therefore, enterprises should comprehensively evaluate their budget and post-purchase costs to select the most cost-effective equipment.
III. Optimization Strategies for Different Industries
(A) Customized Configuration to Enhance Equipment Adaptability
Each industry can customize the configuration of plate and frame filter presses according to its own production characteristics. For example, the chemical industry can add anti-corrosion coatings and equip the equipment with online detection systems to monitor material leakage in real-time. The food industry can customize filter plates with special shapes to facilitate material flow and separation. The mining industry can install wear-resistant protective sleeves and optimize the layout of inlet pipes to improve the equipment's wear resistance and processing efficiency. The wastewater treatment industry can configure sludge conditioning devices to improve sludge dewatering performance. Through customized configurations, the equipment can better meet the production needs of different industries and achieve optimal performance.
(B) Optimizing Operation Processes to Ensure Efficient Operation
Scientific and reasonable operation processes should be formulated based on the production rhythms of different industries. For instance, in the chemical industry with continuous production, the start-stop sequence of the equipment can be optimized to reduce idle time and lower energy consumption. In the food industry, when changing product batches, standardized equipment cleaning and disinfection processes should be followed to ensure product quality and safety. In the mining industry, filtration pressure, feeding speed, and other parameters can be adjusted in real-time according to changes in ore properties to improve separation effects. In the wastewater treatment industry, squeezing time and pressure can be flexibly adjusted according to fluctuations in sludge water content to achieve efficient dewatering. Meanwhile, strengthening operator training to enable them to master equipment operation skills and troubleshooting methods is also key to ensuring the stable operation of the equipment.
IV. Conclusion and Outlook
Only by fully considering industry characteristics and optimizing the selection and use of plate and frame filter presses can these devices achieve efficient and stable operation, creating greater value for enterprises across different industries. In the future, with the continuous emergence of new materials and technologies, plate and frame filter presses will play an even more important role in emerging industries such as new energy and biopharmaceuticals. Their equipment performance will also continue to upgrade, moving towards intelligence, high efficiency, and environmental friendliness to better meet the growing production needs and environmental requirements of various industries.
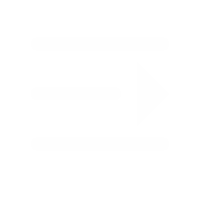
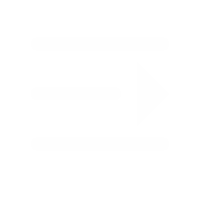
—— Contact:Manager
—— Tel:+86 16632826789
—— Email:sales@hbscfilterpress.com
—— Url:https://www.hbscfilterpress.com
—— Address:West Zone of Economic Development Zone, Fucheng County, Hengshui City, Hebei Province