NewsDetails
Troubleshooting Common Issues of Plate and Frame Filter Press: Quick Solutions for Blockages, Leaks, and More
author:Shuangcheng time:2025-06-15 04:16:45 Click:82
In industrial production, the Plate and Frame Filter Press stands out as a crucial piece of equipment across various industries due to its exceptional solid-liquid separation capabilities. However, after prolonged operation, the machine is prone to various malfunctions. Once a fault occurs, it can significantly reduce production efficiency, increase maintenance costs and material waste, and even disrupt the stability of the entire production process. Therefore, the ability to quickly and accurately identify and resolve faults is vital for ensuring the normal operation of the equipment and minimizing production losses.
I. Common Fault Types and Efficient Troubleshooting Solutions
(1) Filter Cloth and Filter Plate Blockage
Fault Symptoms: During equipment operation, the filtration rate slows down noticeably, failing to achieve the expected processing volume within the set filtration time. Additionally, the operating pressure of the equipment continues to rise abnormally, far exceeding the normal working pressure range, and may even trigger the pressure protection device to alarm and shut down the machine.
Possible Causes: The properties of the material itself are a significant factor. For instance, high-viscosity materials tend to adhere to the surfaces of the filter cloth and filter plates, while large particles can easily block the pores of the filter cloth. Improper selection of the filter cloth, such as an inappropriate pore size or material that does not match the material being processed, can also hinder effective filtration. Moreover, inadequate daily cleaning and maintenance can lead to the accumulation of residual materials on the filter cloth and filter plates, which dry and harden over time, further obstructing the filtration process.
Solutions: Adjust the filtration process parameters according to the material properties. For example, reduce the feed rate or increase the filtration temperature to improve the material's fluidity. Promptly replace the filter cloth with one that is suitable for the material, selecting the appropriate pore size and material. Strengthen cleaning and unclogging efforts. After each filtration operation, rinse the filter plates and filter cloth with high-pressure water promptly. If necessary, soak them in a specialized cleaning agent to ensure thorough cleaning and unobstructed operation.
(2) Equipment Leakage
Fault Symptoms: Leakage of material occurs at the joints between filter plates, pipeline connections, and other areas, resulting in environmental pollution, material waste, and possibly abnormal sounds during equipment operation.
Possible Causes: Long-term use of the filter plates can cause wear on the sealing surfaces, making them uneven and affecting the sealing effect. Sealing components, such as sealing rings and gaskets, may age, deform, or lose elasticity, leading to ineffective sealing. Insufficient pressure in the hydraulic system may prevent the filter plates from being tightly pressed together, allowing material to seep through the gaps.
Solutions: Repair the worn sealing surfaces of the filter plates. If the wear is severe, replace the filter plates promptly. Regularly inspect the sealing components and replace any that are aged or damaged immediately. Adjust the hydraulic system pressure to ensure it meets the normal operating requirements of the equipment, enabling the filter plates to be securely pressed together.
(3) Hydraulic System Faults
Fault Symptoms: The filter plates fail to press together normally, preventing the equipment from entering the filtration process. The hydraulic system pressure is unstable, fluctuating between high and low levels, which affects the normal operation and filtration effect of the equipment.
Possible Causes: Insufficient hydraulic oil in the system can lead to a lack of power for normal operation. Prolonged use of the hydraulic oil can cause it to deteriorate or become contaminated, resulting in poor system performance. A malfunctioning hydraulic pump, such as internal component wear or poor sealing, can affect pressure output. Leaks in the hydraulic piping can cause pressure loss.
Solutions: Regularly check the hydraulic oil level and top it up promptly when necessary. Replace the hydraulic oil according to the equipment's usage requirements to ensure oil quality. Inspect and repair the hydraulic pump, replacing worn components and fixing sealing issues. If the pump is severely damaged, replace it with a new one. Carefully examine the hydraulic piping to locate and repair any leaks, ensuring good sealing performance.
(4) Electrical System Faults
Fault Symptoms: The equipment fails to start after being powered on. Control components, such as buttons and indicators, malfunction and do not respond to operations. The equipment may suddenly stop during operation, and the control system displays abnormal fault codes.
Possible Causes: Short circuits or open circuits in the electrical wiring can disrupt the normal flow of current. Motor failures, such as damaged windings or seized bearings, can affect equipment operation. Damaged sensors may fail to transmit signals accurately, causing the control system to misjudge and trigger equipment faults.
Solutions: Use professional tools to conduct a comprehensive inspection of the electrical wiring and repair any short circuits or open circuits. Inspect and repair the motor, replacing damaged windings, bearings, and other components. If the motor is beyond repair, replace it with a new one. Check the sensors and replace any that are damaged promptly to ensure accurate signal transmission and normal operation of the control system.
II. Fault Prevention Measures
(1) Routine Maintenance
Establish a comprehensive routine maintenance system. Regularly clean all components of the equipment to remove dust, oil, and residual materials from the surfaces. Carefully inspect key areas such as filter plates, filter cloths, hydraulic systems, and electrical systems for signs of wear, aging, or looseness. Identify and address potential issues promptly.
(2) Standardized Operating Procedures
Operators must strictly follow the equipment operation manual when starting, stopping, and operating the equipment. Before starting the equipment, prepare all necessary items and check the condition of the material, power supply, and hydraulic oil. During operation, closely monitor the equipment's operating parameters, such as pressure, flow rate, and temperature, and make adjustments promptly if abnormalities are detected. After stopping the equipment, follow the prescribed steps for cleaning and maintenance to ensure the equipment remains in good condition.
(3) Regular Replacement of Key Components
Based on the equipment's usage and the service life of its components, establish reasonable replacement cycles for key components such as filter cloths, sealing components, and hydraulic oil. Even if components do not show obvious signs of damage, replace them promptly upon reaching the replacement cycle to prevent equipment failures caused by aging or performance degradation.
III. Conclusion
The stable operation of the Plate and Frame Filter Press in industrial production relies on the rapid identification and effective resolution of common faults, as well as the implementation of scientific preventive measures. Each type of fault, from filter cloth and filter plate blockages to equipment leaks, hydraulic system issues, and electrical system malfunctions, has its unique symptoms, causes, and solutions. Additionally, by implementing routine maintenance, standardized operating procedures, and regular replacement of key components, the probability of equipment failures can be effectively reduced. Only by placing importance on fault identification and prevention can we ensure the continuous and efficient operation of the plate and frame filter press, providing a solid guarantee for production.
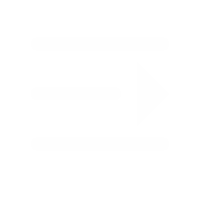
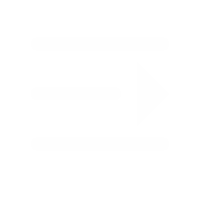
—— Contact:Manager
—— Tel:+86 16632826789
—— Email:sales@hbscfilterpress.com
—— Url:https://www.hbscfilterpress.com
—— Address:West Zone of Economic Development Zone, Fucheng County, Hengshui City, Hebei Province